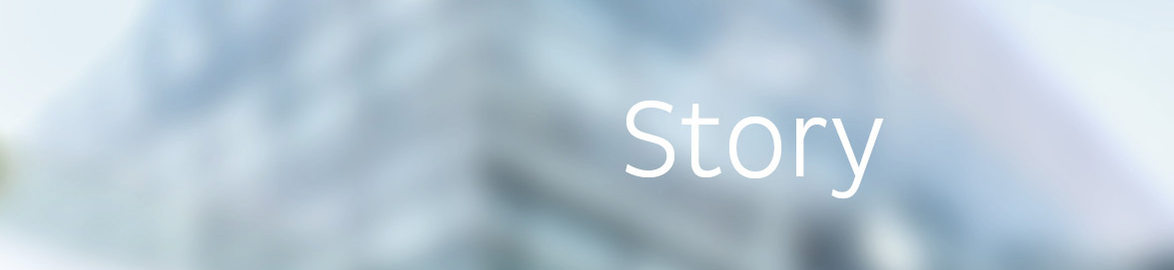
Über eine Milliarde Tonnen Schadstoffe weniger
22.03.2017 — Heute fahren weltweit über eine Milliarde Fahrzeuge auf den Straßen, schon bis 2018 soll sich die Zahl auf 1,2 Milliarden erhöhen. Abgaskatalysatoren der BASF Catalysts Germany GmbH aus dem niedersächsischen Nienburg sorgen dafür, dass der größte Teil der entstehenden Schadstoffe gar nicht erst in die Luft gelangt. Für die Sicherheit am Produktionsstandort sorgen die Mitarbeiter von Dussmann Service.
Appetitlich sieht das nicht aus; der Name sagt alles: In den Bottichen schwappt die „Slurry“, zu Deutsch „Schlamm“. Kostbarer Schlamm: Gleich drei Edelmetalle sind darin enthalten, Rhodium, Palladium und Platin. Mit ihnen werden die Rohlinge aus Keramik bzw. Metall beschichtet, die später den Fahrzeugkatalysator ausmachen und schädliche Abgase umwandeln. Von eimergroß bis fingerhutklein reichen die Größen, je nachdem, ob ein tonnenschwerer Lkw ausgerüstet werden soll oder ein kleines Mofa.
Weltweiter Marktführer im Bereich Katalysator- Technologien ist der Unternehmensbereich Catalysts der BASF. In praktisch allen namhaften Automarken verwandeln Katalysatoren der BASF-Tochter Kohlenmonoxid, Stickoxide und unverbrannte Kohlenwasserstoffe in Wasser, Stickstoff und Kohlendioxid. Über 95 Prozent der Abgasstoffe werden damit eliminiert (mehr dazu im Kasten, S. 17). Die Hauptverwaltung des europäischen Autokatalysatorgeschäfts der BASF sitzt mit Forschung und Vertrieb in Hannover. Produziert wird in Nienburg/Weser.
Für jeden Topf den passenden Deckel
Für jeden Motor und seine jeweiligen Emissionen muss der passende Katalysator gefunden werden. Hier beginnt die Herausforderung: Denn selbst innerhalb eines einzelnen Automodells haben Käufer die Wahl zwischen zahlreichen verschiedenen Motorisierungen – das bedeutet auch verschiedene Abgaszusammensetzungen und damit jeweils andere Katalysatoren.
Die Fachleute von BASF kennen sich damit aus. „Spannend wird es, wenn ein Autohersteller kurzfristig eine Bestellung ändert“, erklärt Dr. Martin Kraum, Werkleiter des BASF-Emissionskatalysatoren-Werks in Nienburg. „Dann bleiben uns manchmal nur 14 Tage Zeit, um die Maschine umzurüsten, die Rohlinge zu bestellen und die Beschichtung anzupassen.“
Heute kaum vorstellbar – Schadstoffe vor 40 Jahren
Viel ist bereits erreicht worden: 100 Autos stoßen heute etwa die gleiche Schadstoffmenge aus, die im Jahr 1974 noch ein einziges Fahrzeug produzierte, also vor Einführung des Kats. Trotzdem lautet die Frage: Wie lassen sich noch mehr Schadstoffe reduzieren bei noch geringerem Materialverbrauch? An zwei Stellschrauben können die Experten drehen: beim Rohling und bei seiner Beschichtung. „Je feiner die Kanäle, durch die die Abgase strömen, umso mehr schädliche Partikel können umgesetzt werden“, weiß Werkleiter Kraum. „Wenn es jedoch zu eng wird, dann ist das wie bei einem Läufer, dem man den Hals zudrückt. Richtig gut atmen kann der dann nicht mehr.“ Größter Gegner für die Entwickler ist die Hitze, die in und um den Katalysator während des Fahrens entsteht. Bis über 1.000 Grad Celsius wird ein Katalysator heiß, und auch dann müssen die aufgebrachten Metalle halten. Mehr als 160.000 Kilometer Laufleistung verlangt der Gesetzgeber von einem Katalysator.
Im Motorentestlabor der BASF Catalysts Germany GmbH in Hannover erproben Forscher neue Produkte und Technologien an Motorenprüfständen. Hier werden Katalysatoren unter verschiedensten Bedingungen getestet und unterschiedlichen Stresstests ausgesetzt. Unter anderem durch diesen Forschergeist entstand der neuartige EMPRO FWCTM Vier-Wege-Katalysator. Er kombiniert die Leistungen eines modernen Drei-Wege-Katalysators mit einem Rußpartikelfilter. Dieser Katalysator ermöglicht es, die neuen Euro-6c-Grenzwerte einzuhalten, während negative Effekte auf die Leistung und den Verbrauch des Motors minimiert werden.
Solche Erfolge sind auch das Ergebnis des starken Unternehmensverbunds, zu dem der Katalysatorhersteller gehört. 2006 kaufte BASF, das größte Chemieunternehmen der Welt, den US-amerikanischen Hersteller Engelhard Corporation, den Erfinder des ersten kommerziellen Drei-Wege- Katalysators. Dessen Mitarbeiter trafen auf Gleichgesinnte innerhalb der BASF-Gruppe, mit ebenso viel Begeisterung und Kompetenz im Automobilsektor, ganz gleich ob es sich um Lacke, Kunststoffe, Karosserien oder Batterien handelt.
Sicher ist sicher
Klar, dass bei so viel Entwicklungsleistung, teuren Edelmetallen und den besonderen Herausforderungen chemischer Produktion die Sicherheit vor Ort eine große Rolle spielt. Seit Juli 2014 sorgt das Team von Dussmann Service dafür, dass nur Befugte auf das Werkgelände der BASF Catalysts Germany in Nienburg gelangen, dass in der Produktion keine Sicherheitsrisiken lauern und dass niemand und nichts unbemerkt das Gelände verlässt. Rund zehn Mitarbeiter sind dafür rund um die Uhr, 365 Tage im Jahr im Einsatz.
Seit Januar 2016 können sie auf neueste Sicherheitstechnik zugreifen. Über ein Jahr lang wurde der gesamte Eingangsbereich umgebaut, eines der ersten Projekte des damals neuen Security Managers in Nienburg, Ulrich W. Müller. „Jedes Fahrzeug und jede Person wird beim Betreten und Verlassen des Geländes kontrolliert und elektronisch registriert“, beschreibt Müller eine der Aufgaben. „Auf unseren hochmodernen Gepäckscanner wäre mancher Flughafen sicherlich neidisch.“
Alle ein- und ausfahrenden Fahrzeuge müssen inzwischen eine Schleuse mit zwei aufeinanderfolgenden Toren passieren. Eine elektronische Sperre sorgt dafür, dass immer nur ein Tor gleichzeitig geöffnet werden kann. Drei Mitarbeiter am Empfang kontrollieren die Verkehrssicherheit des Fahrzeugs, die Lieferpapiere, die Ladung. „Wir haben schon die verrücktesten Dinge aus den Fahrzeugen herausgeholt“, schmunzelt Dussmann-Objektleiter David Klijnstra. „Große Messer etwa unterm Vordersitz. Auch abgefahrene Reifen oder ein abgelaufener TÜV sind Sicherheitsrisiken, mit denen das Fahrzeug nicht aufs Gelände kommt.“ Es ist ein Balanceakt zwischen der nötigen Gründlichkeit und der Aufgabe, den Verkehr aus Lkws, Pkws und Gabelstaplern am Fließen zu halten.
Für alle Besucher sind die Dussmann-Mitarbeiter der erste Kontakt bei der BASF Catalysts Germany. Sie haben für jeden ein freundliches Wort, sei es am Empfang oder in der Telefonzentrale. Auch die Verteilung von an die Hausadresse gerichteten Mails und die Poststelle gehören zu den Aufgaben der Mannschaft. Videokameras in der Produktion und auf dem gesamten Außengelände liefern rund um die Uhr aktuelle Bilder in die Zentrale.
Der Nienburger Sicherheitschef Müller ist mit dem Dussmann-Team zufrieden. „Wir haben die gleiche Vorstellung davon, wie Dinge gehandhabt werden müssen, und ziehen an einem Strang – für optimale Sicherheit am Standort“, beschreibt er die Zusammenarbeit. Abstimmungen geschehen unkompliziert und im Wortsinne auf kurzem Weg. Bei den Umbauplanungen hat Müller darauf geachtet, dass sein Büro direkt am Besucherempfang platziert wurde.
Dass sie ihren Job gut machen, wurde vor Kurzem auch von oberster BASF-Stelle anerkannt: Bei einem Audit mit Experten von der Konzernmutter aus Ludwigshafen fanden die Abläufe in Nienburg viel Lob.
Dussmann Newsroom
Aktuelles
News, Stories, Downloads und aktuelle Events – alles zu Dussmann sowie den Geschäftsbereichen Facility Management, Food Services und Technical Solutions finden Sie im Newsroom. Schauen Sie rein und lernen Sie uns besser kennen!